Solutions
Tool Technical Support and User Guide
We provide detailed information, usage recommendations, maintenance tips, and frequently asked questions (FAQ) for the four core tools — Carbide Endmill, Turning Tool, Carbide Insert, and Drill Bit. If you have any questions regarding cutting tools, feel free to contact us. We are available 24/7 to assist you with any inquiries.
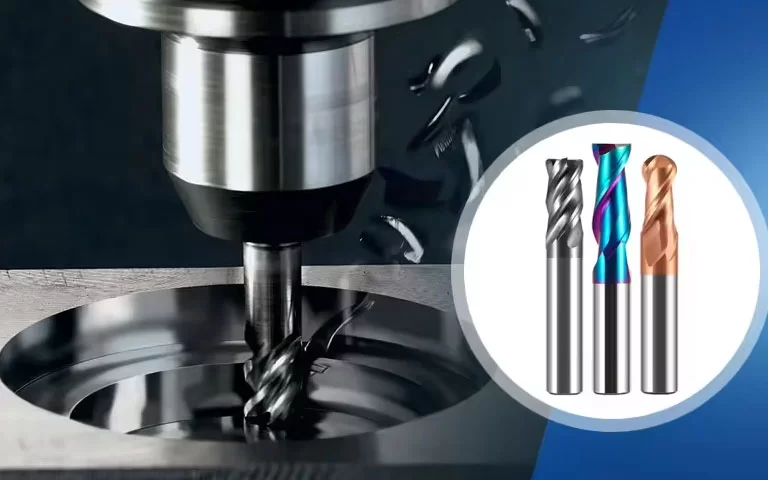
Carbide Endmill
Applications: Widely used in milling processes, such as mold making, metal cutting, and high-precision part manufacturing.
Features: High hardness, wear resistance, heat resistance, suitable for high-speed cutting.
Industries: Aerospace, automotive, precision mold making, metalworking, and more.
Common Specifications:
- Tool diameter, cutting depth
- Coating types (e.g., TiAlN, TiN, etc.)
- Geometric shapes (ball end mill, flat end mill, etc.)
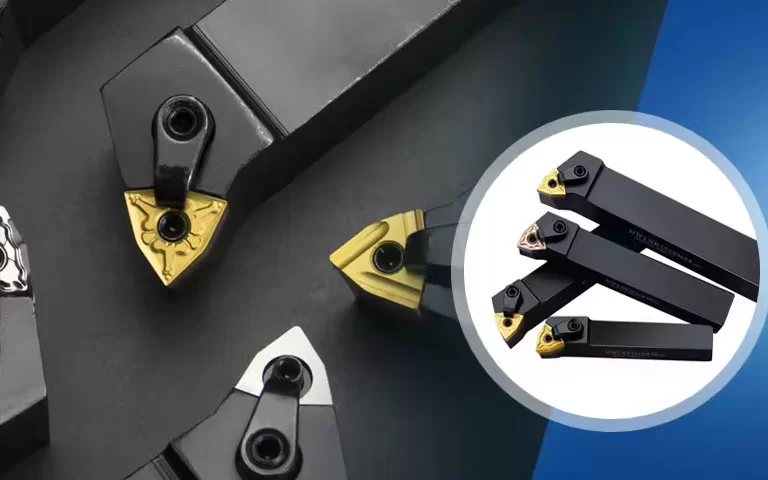
Turning Tool
Applications: Used in lathes for external and internal turning, grooving, threading, and other processes.
Features: Strong heat resistance, suitable for high-speed turning, adaptable to a wide range of materials.
Industries: Precision turning, automation production, mold making, and more.
Common Specifications:
- Insert geometry (square, triangle, round, etc.)
- Materials (carbide, ceramics, etc.)
- Coatings (e.g., TiC, TiN, etc.)
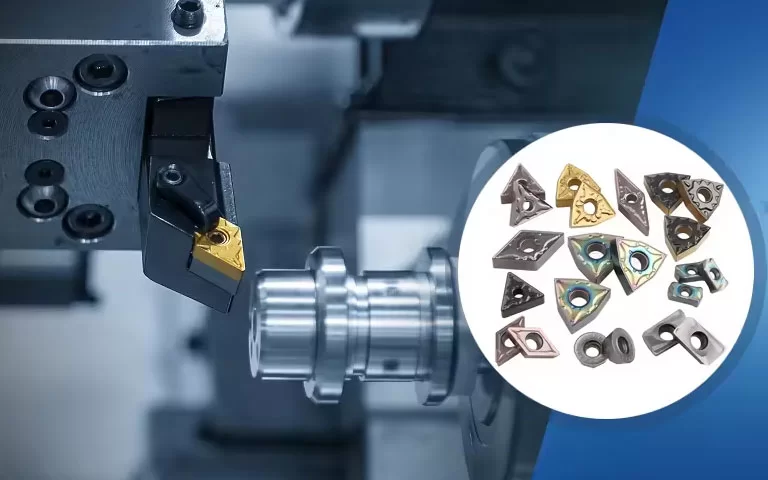
Carbide Insert
Applications: Replaceable cutting parts for turning and milling tools, used in various cutting processes.
Features: High strength, high wear resistance, easy to replace, improving production efficiency.
Industries: Turning, milling, drilling, and more.
Common Specifications:
- Geometries (square, triangle, etc.)
- Insert materials (carbide, coated inserts, etc.)
- Tool wear-resistant coatings
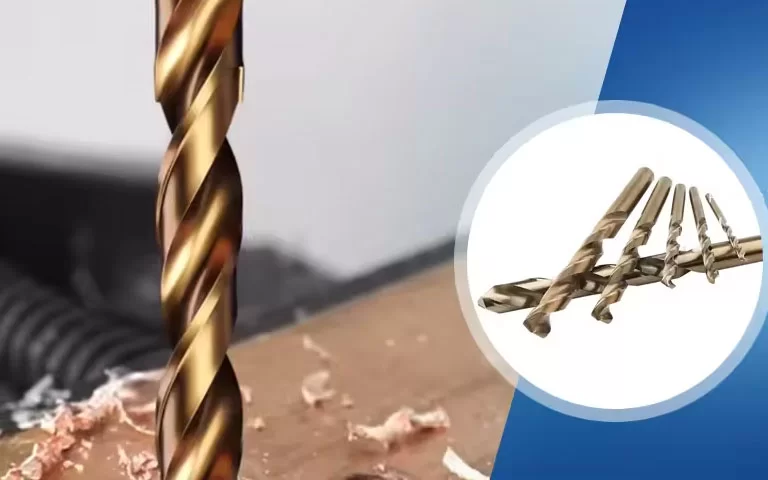
Drill Bit
Applications: Used for precision drilling, deep hole machining, and applicable to different materials.
Features: Heat resistance, high hardness, suitable for a variety of materials, including steel, aluminum alloy, copper, plastics, etc.
Industries: Metal drilling, plastic drilling, wood drilling, and more.
Common Specifications:
- Drill bit diameter, length, coatings, etc.
- HSS and carbide drill bits
Tool Usage Recommendations
- Choosing the Right Tool : Choose tools based on material and cutting conditions to ensure optimal performance.
- Optimizing Cutting Parameters : Adjust speed, feed, and depth to prolong tool life and improve efficiency.
- Using Coolants : Use the right coolant to lower temperatures and reduce wear.
- Tool Replacement & Resharpening: Regularly check and replace or resharpen tools to maintain machining accuracy.
Tool Maintenance and Care
- Cleaning: Clean tools after use to remove residues and prevent scratches.
- Storage: Store tools in a dry, moisture-free environment to avoid rusting.
- Coating Maintenance: Replace damaged coatings to maintain tool durability.
- Checking Sharpness: Regularly inspect and resharpen dull tools for optimal performance.
F.A.Q.
Frequently Asked Questions
When selecting tool materials, consider the hardness of the workpiece, cutting conditions, and type of machining. Carbide tools are suitable for harder metals, while HSS (High-Speed Steel) tools are better for general metalworking.
Tool heating may be caused by excessive cutting speed or insufficient coolant. It is recommended to reduce the cutting speed and ensure adequate coolant supply. Use the appropriate coolant to effectively dissipate heat.
Tool life depends on various factors such as the material being cut, process parameters, frequency of use, and cutting depth. Proper adjustment of cutting conditions and regular maintenance can significantly extend tool life.
Tool coatings primarily provide wear resistance, oxidation resistance, and reduced friction. Common coatings like TiN and TiAlN improve the tool’s heat resistance and extend its service life.
Tool chipping may be caused by incorrect cutting parameters, insufficient cooling, or excessive cutting forces. Check and adjust the cutting conditions, optimize feed rates, and ensure effective coolant usage. If the issue persists, consider replacing or resharpening the tool.