Disc Milling Cutter
- Usage: External Turning Tool
- Hardness: Below HRC40
- Coating: CVD
- Place of Origin: Shandong, China
- Customized Support: OEM, ODM
- Brand Name: CF
- Model Number: CCMT09T304 LF6018
- Selling Units: Single item
- Package Size: 15X5X5 cm
- Gross Weight: 0.200 kg
Don’t see what you’re looking for? Let us help you. Give us a WhatsApp or send us a message.You can contact us by:
Feature | Description |
---|---|
High Precision and Durability | The CF Tungsten steel Carbide T cutter milling cutter offers high precision and durability, ensuring long-lasting performance in high-speed cutting. |
Customization Options | CF provides OEM and ODM customization support to meet specific needs and requirements for different industries or user specifications. |
Multi-Material Compatibility | This milling cutter works with various materials, such as aluminum alloy, copper, and plastic, making it versatile for different machining tasks. |
Wide Compatibility | The CF milling cutter integrates smoothly with milling machines, CNC equipment, and lathes, fitting into existing production workflows. |
High-Speed Cutting Capability | Built with tungsten steel carbide, the CF milling cutter is designed for efficient high-speed cutting, delivering precise results on complex workpieces. |
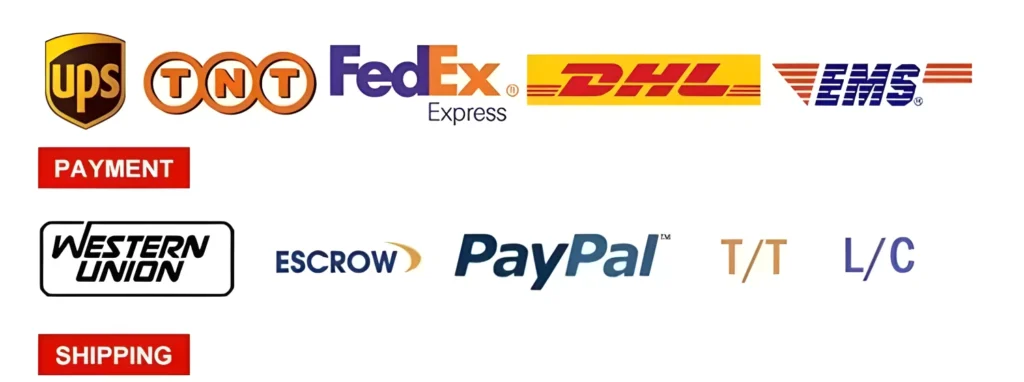
Lead time ( 1 - 200 boxes ) | 5days |
---|---|
Lead time ( 201 - 1000 boxes ) | 10days |
Lead time ( 1001 - 5000 boxes ) | 15days |
Lead time (5000 + boxes ) | 30days |
Support samples | YES! |
F.A.Q.
Frequently Asked Questions
When selecting tool materials, consider the hardness of the workpiece, cutting conditions, and type of machining. Carbide tools are suitable for harder metals, while HSS (High-Speed Steel) tools are better for general metalworking.
Tool heating may be caused by excessive cutting speed or insufficient coolant. It is recommended to reduce the cutting speed and ensure adequate coolant supply. Use the appropriate coolant to effectively dissipate heat.
Tool life depends on various factors such as the material being cut, process parameters, frequency of use, and cutting depth. Proper adjustment of cutting conditions and regular maintenance can significantly extend tool life.
Tool coatings primarily provide wear resistance, oxidation resistance, and reduced friction. Common coatings like TiN and TiAlN improve the tool’s heat resistance and extend its service life.
Tool chipping may be caused by incorrect cutting parameters, insufficient cooling, or excessive cutting forces. Check and adjust the cutting conditions, optimize feed rates, and ensure effective coolant usage. If the issue persists, consider replacing or resharpening the tool.
Reviews
There are no reviews yet.